Help your fellow builder by leaving your feedback based on these three criteria:
- Originality: How original is this - never seen before?
- Building Techniques: How much skill do you think the creator of this MOC has, in terms of building technique?
- Details: Express how much you like the details of the build.
Your feedback is only shown to the creator as well as yourself. It is not available for other users to see. The creator won't see your user name.
The Power Functions and NXT themes each include a LiPo rechargeable battery in the range. These need a plug-in charger, which means you have to either tether the model to the charger or remove the battery from the model when it is being charged.
It is desirable for a Train, remote-controlled car, Technic model or NXT-based robot to be able to recharge the battery wirelessly. This means it can happen automatically and the user does not have to handle the model, battery or charger. The model can locate itself by a charging device either automatically or under user remote control and the charging will happen automatically.
Inductive charging systems exist for mobile phones and tablets. These use a coil in a pad on the desk (the static coil) and another coil in the phone or its case (the mobile coil). The phone is placed on the pad to put the two coils close together.
My idea is for a single new LEGO piece, an inductive charging coil device. This consists of a tile 4M x 4M x 2 plates high, containing an electrical coil of many turns, up to 30mm in diameter, oriented so that the magnetic field emanates from the top smooth surface of the coil device. It may alternatively use multiple coils to achieve the same effect efficiently.
The device contains all circuitry necessary for the conversion of power between 10V DC 700mA and a high frequency AC signal used for the inductive power transfer. For a single device to perform the transmission and reception roles an automatic circuit would either produce AC from DC or DC from AC depending on whether the DC cable input or AC coil reception provided a greater signal. This means that the use in the two roles will be transparent to the user. The internal circuit design has to consider the use of several devices in parallel so that its Tx/Rx role state would not be disrupted by a signal from a parallel device. In the extreme a tiny role switch may be permitted but must be incorporated in the body of the device and any user error in switch position must result in a safe state, with any failure of the system to work being easily rectified according to the instructions.
The device incorporates a suitable wire and plug such that it can connect to the charger at one end and the battery at the other end. A wire similar in length to that of the Power Functions IR Receiver is suggested. The plug may be a standard power supply plug of a type compatible with the existing charger and battery socket. A standard power supply adapter plug may be used in order to keep the two coil devices the same and hence minimise product cost. If both a plug and a socket were wired to the flying lead then not only would there be no need for a separate adapter but a number of coils could be connected easily in parallel, allowing better efficiency or easier targeting for the train or robot stopping place.
The underside of the coil device would have the usual plate-depth stud recesses over the 4x4 area so that, in the Train application, it could be fixed between the rails of standard 9-Volt or Power Functions straight railway track pieces without any part of it protruding above the rail height - see main picture. This is essential to enable motors and couplings to travel over it.
Another coil device exactly the same would be slung upside-down under a railway carriage. SNOT techniques are already used in sets in this location e.g. the Santa Fe loco. This means that the smooth surfaces of the two coil devices might be only 1mm apart when the train stands over the fixed coil. Minimising this gap maximises the efficiency of transfer of charging current and minimises the charging time. Ideally the device, or multiple similar devices in parallel, would be able to handle the 700mA charging current of the existing charger. If there is any restriction then it must be transparent to the user and be safe for an unlimited time, with the only consequence being a longer charging time.
In the Technic and Mindstorms applications the static coil device could be fixed at any convenient angle as a drive-over, drive-up-to, drive under or drive-past charging station. Alternatively a model might hit a button or trigger for a crane to lower the static coil onto the model's coil.
In a Mindstorms application the monitoring of the battery voltage could be used to command the robot to leave the charging station or trigger it to remove the static coil from the robot's coil. This sort of charging cycle could form part of a competition challenge.
In any application it would be possible to rotate the model's coil over the static coil whilst maintaining inductive power transfer. This could be used in a crane or turret application where the battery in the rotating turret can charge from the static coil in the base.
The product could be sold either as a single coil device in a similar way to the Power Functions IR Receiver, or as a twin coil pack with a plug adapter if one were needed. A plug and socket on the flying lead is preferable because it makes it so easy to use multiple devices in parallel.
The market spanning Power Functions cars and trains as well as Technic and Mindstorms should allow the product cost to be reasonable. A cost of £10 to £15 should be achievable, in proportion to the charger and battery cost.
I believe this device could be the making of Power Function Trains because it would allow more autonomy. A train would do a circuit, stop over the coil and charge up without any additional user intervention. Using coils in parallel allows several tracks to have charging coils in a yard of through-sidings, allowing trains to be run in turn at an exhibition. This would bring Power Function Trains up to the exhibition autonomy of 9-Volt and 12-Volt trains. This allows the exhibitors to talk to the public more, enhancing their experience and selling more LEGO trains.
Images:
Main picture: A straight track piece with tiles 2 plates high and 4M wide. These ight be 4M long for a single coil or 16M long for 4 coils. This could be separate coil devices or a multiple-coil device. A 4m x 8M device with 2 coils would fit the train application. Other applications may be able to accommodate this too.
Picture 1: The wagon standing over the coil. The mobile coil wire goes up through the carriage base to connect to the LiPo battery. The static coil wire comes out from beneath the track to connect to the charger.
Picture 2: The gap between the static coil between the rails and the mobile coil on the train should be minimised so that the charging current transfer is most efficient. A 1mm gap is suggested in order to provide consistent clearance for the train to move.
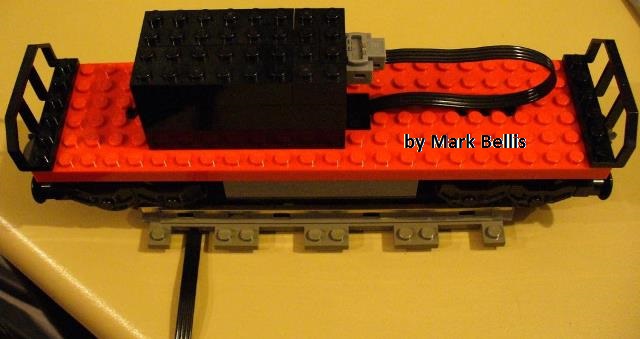
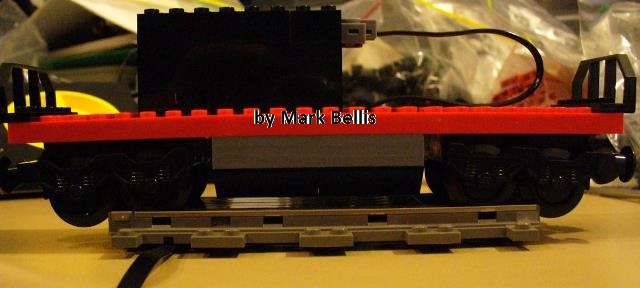
It is desirable for a Train, remote-controlled car, Technic model or NXT-based robot to be able to recharge the battery wirelessly. This means it can happen automatically and the user does not have to handle the model, battery or charger. The model can locate itself by a charging device either automatically or under user remote control and the charging will happen automatically.
Inductive charging systems exist for mobile phones and tablets. These use a coil in a pad on the desk (the static coil) and another coil in the phone or its case (the mobile coil). The phone is placed on the pad to put the two coils close together.
My idea is for a single new LEGO piece, an inductive charging coil device. This consists of a tile 4M x 4M x 2 plates high, containing an electrical coil of many turns, up to 30mm in diameter, oriented so that the magnetic field emanates from the top smooth surface of the coil device. It may alternatively use multiple coils to achieve the same effect efficiently.
The device contains all circuitry necessary for the conversion of power between 10V DC 700mA and a high frequency AC signal used for the inductive power transfer. For a single device to perform the transmission and reception roles an automatic circuit would either produce AC from DC or DC from AC depending on whether the DC cable input or AC coil reception provided a greater signal. This means that the use in the two roles will be transparent to the user. The internal circuit design has to consider the use of several devices in parallel so that its Tx/Rx role state would not be disrupted by a signal from a parallel device. In the extreme a tiny role switch may be permitted but must be incorporated in the body of the device and any user error in switch position must result in a safe state, with any failure of the system to work being easily rectified according to the instructions.
The device incorporates a suitable wire and plug such that it can connect to the charger at one end and the battery at the other end. A wire similar in length to that of the Power Functions IR Receiver is suggested. The plug may be a standard power supply plug of a type compatible with the existing charger and battery socket. A standard power supply adapter plug may be used in order to keep the two coil devices the same and hence minimise product cost. If both a plug and a socket were wired to the flying lead then not only would there be no need for a separate adapter but a number of coils could be connected easily in parallel, allowing better efficiency or easier targeting for the train or robot stopping place.
The underside of the coil device would have the usual plate-depth stud recesses over the 4x4 area so that, in the Train application, it could be fixed between the rails of standard 9-Volt or Power Functions straight railway track pieces without any part of it protruding above the rail height - see main picture. This is essential to enable motors and couplings to travel over it.
Another coil device exactly the same would be slung upside-down under a railway carriage. SNOT techniques are already used in sets in this location e.g. the Santa Fe loco. This means that the smooth surfaces of the two coil devices might be only 1mm apart when the train stands over the fixed coil. Minimising this gap maximises the efficiency of transfer of charging current and minimises the charging time. Ideally the device, or multiple similar devices in parallel, would be able to handle the 700mA charging current of the existing charger. If there is any restriction then it must be transparent to the user and be safe for an unlimited time, with the only consequence being a longer charging time.
In the Technic and Mindstorms applications the static coil device could be fixed at any convenient angle as a drive-over, drive-up-to, drive under or drive-past charging station. Alternatively a model might hit a button or trigger for a crane to lower the static coil onto the model's coil.
In a Mindstorms application the monitoring of the battery voltage could be used to command the robot to leave the charging station or trigger it to remove the static coil from the robot's coil. This sort of charging cycle could form part of a competition challenge.
In any application it would be possible to rotate the model's coil over the static coil whilst maintaining inductive power transfer. This could be used in a crane or turret application where the battery in the rotating turret can charge from the static coil in the base.
The product could be sold either as a single coil device in a similar way to the Power Functions IR Receiver, or as a twin coil pack with a plug adapter if one were needed. A plug and socket on the flying lead is preferable because it makes it so easy to use multiple devices in parallel.
The market spanning Power Functions cars and trains as well as Technic and Mindstorms should allow the product cost to be reasonable. A cost of £10 to £15 should be achievable, in proportion to the charger and battery cost.
I believe this device could be the making of Power Function Trains because it would allow more autonomy. A train would do a circuit, stop over the coil and charge up without any additional user intervention. Using coils in parallel allows several tracks to have charging coils in a yard of through-sidings, allowing trains to be run in turn at an exhibition. This would bring Power Function Trains up to the exhibition autonomy of 9-Volt and 12-Volt trains. This allows the exhibitors to talk to the public more, enhancing their experience and selling more LEGO trains.
Images:
Main picture: A straight track piece with tiles 2 plates high and 4M wide. These ight be 4M long for a single coil or 16M long for 4 coils. This could be separate coil devices or a multiple-coil device. A 4m x 8M device with 2 coils would fit the train application. Other applications may be able to accommodate this too.
Picture 1: The wagon standing over the coil. The mobile coil wire goes up through the carriage base to connect to the LiPo battery. The static coil wire comes out from beneath the track to connect to the charger.
Picture 2: The gap between the static coil between the rails and the mobile coil on the train should be minimised so that the charging current transfer is most efficient. A 1mm gap is suggested in order to provide consistent clearance for the train to move.
Picture 1: The wagon standing over the coil. The mobile coil wire goes up through the carriage base to connect to the LiPo battery. The static coil wire comes out from beneath the track to connect to the charger.
Picture 2: The gap between the static coil between the rails and the mobile coil on the train should be minimised so that the charging current transfer is most efficient. A 1mm gap is suggested in order to provide consistent clearance for the train to move.